MARINE & OFFSHORE EQUIPMENT
- Dredging Equipment
- Marine Deck Machinery
-
Marine Mooring Equipment
-
Marine Anchor
- AC-14 HHP Anchor
- Admiralty Anchor
- Beldt Stockless Anchor
- Bruce Anchor
- Spek Anchor
- Danforth HHP Anchor
- Delta High Holding Power Anchor
- GB11579-89 Light Weight Anchor
- Hall Anchor
- High Holding Power Mastrosov Anchor
- Hot Dip Galvanized Anchor
- Japan Stock Anchor
- JIS Stockless Anchor
- Pool Anchor
- Single Fluke Anchor
- Stainless Steel Anchor
- Stevpris MK5 Anchor
- Stingray Anchor
- US Navy Stockless Anchor
-
Marine Anchor Chain
-
Marine Shackle
- Kenter Shackle
- D Type Joining Shackle
- Pear Shaped Shackle
- Anchor Swivel Shackle Type A
- Anchor Swivel Shackle Type B
- Buoy Shackle Type A
- Buoy Shackle Type B
- C Type Detachable Connecting Link
- D Shackle
- Forelock Shackle
- Anchor Chain Swivel Group
- Straight Shackle
- Anchor Shackle
- Marine Triangle Plate
- Anchor Chain Swivel
- Anchor Chain Joining Shackle
- Anchor Chain End Shackle
- Slim Kenter Shackle
-
Chain Chaser
-
Marine Bollard
-
Marine Chock
-
Marine Fairlead
-
Marine Chain Stopper
-
Marine Mooring Reel
-
Marine Towing Bracket
-
Mooring Rope
-
Marine Towing Hook
-
Marine Shark Jaw
- Marine Fender
-
Marine Buoy
- Marine Floating Pontoon Dock
-
Marine Anchor
- Aquaculture Equipment
- Marine Outfitting Equipment
- Marine Propulsion System
-
Marine Painting
-
Marine Auxiliary Machinery
- Marine Air Compressor
- Marine Air Receiver
- Marine Sewage Treatment Plant
-
Marine Diesel Generator Set
- Marine Oil Water Separator
- Ballast Water Management System
- Marine Hydrophore
- Marine Calorifier
- Seawater Desalination Plant
-
Marine Oil Separator
- Marine Fuel Oil Supply Unit
- Marine Heat Exchanger
-
Marine Hot Well Unit
-
Marine Incinerator
-
Marine Boiler
-
Marine Valve
- JIS Marine Valve
- DIN Marine Valve
- ANSI Marine Valve
- GB Marine Valve
- CB Marine Valve
- CBM Marine Valve
-
Marine Gate Valve
-
Marine Globe Valve
-
Marine Angle Globe Valve
-
Marine SDNR Valve
-
Marine Angle SDNR Valve
-
Marine Check Valve
-
Marine Storm Valve
-
Marine Butterfly Valve
-
Marine Quick Closing Valve
-
Marine Fire Valve
-
Marine Self Closing Valve
- Marine Valve Accessories
-
Marine Pump
- Marine Centrifugal Pump
- Marine Screw Pump
-
Marine Gear Pump
-
Marine Vortex Pump
-
Marine Ejector Pump
-
Marine Diaphragm Pump
-
Marine Piston Pump
-
Marine Fire Pump
-
Marine Emergency Fire Pump
-
Marine External Fire Pump
-
Marine Ballast Water Pump
-
Marine Fuel Pump
-
Marine Lubricating Oil Pump
-
Marine Bilge Pump
-
Marine Sewage Pump
-
Marine Domestic Water Pump
-
Marine General Pump
-
Marine Cargo Oil Pump
-
Marine Hand Pump
- Marine Pump Parts
- Marine Life-saving Equipment
- Fire-fighting Equipment
- Marine Cable
- Marine Electrical Equipment
- Marine HVAC
-
Labour Protection Appliance
- Marine Decorative Material
-
Marine Anode
- Marine Pipe Fitting & Flange
- Marine Instrument
- Ship Building Equipment
INDUSTRY EQUIPMENT
- Hoisting Equipment
- Welding Machine & Material
-
Cutting Machine
- Container Securing Fitting
- Link Chain
- Container & Storage Equipment
-
Diesel Generator Set
- Other Equipment and Tools
- Petrochemical Equipment
- Fiber Reinforced Plastics
- Polymer Materials
- Environmental Protection Series
- Geo-products and Building Materials
- Metal Mesh
- Steel Grating
-
Earthwork Teeth
-
Turnbuckle
STOCK LIST
Contacts
Tel:+86-23-67956606
FAX:+86-23-67956622
Email:manager@cqhisea.com
Working Time: 9:00--17:00
Working Day: Monday to Friday Website: www.cqhisea.com
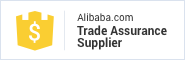
Electric Steam Boiler
Electric Steam Boiler
1. Electric Steam Boiler Description
One of the most important items of equipment aboard ships, boilers are used for numerous purposes. Whether it is steam powered or has a diesel engine as the main form of propulsion, a ship without a boiler is really difficult to imagine. A boiler, in one form or another will be found on a ship. For example if a ship is a steam powered ship, two or more boilers will be provided to produce high temperature, high pressure steam. If a ship is carrying a diesel engine as the main propulsion system, one or two smaller boilers are used for running various ship's machinery and services.
2. Electric Steam Boiler Working Process
A basic boiler is a machine with the simplest arrangement of the internal parts. The main job of a boiler is to make high pressure steam. The feed water supplied to the boiler drum utilizes the heat of the energy released by burning the fuel. This energy of the burning fuel is stored in the form of steam with high temperature and pressure. The fuel is burnt in a combustion chamber inside the boiler.
To attain high efficiency and complete combustion, air is supplied to this combustion chamber through a separate arrangement. The heat generated in this combustion chamber is transferred to the water from the boiler drum through a large surface area, which enables the highest rate of energy transfer.
3. Steam Generation of Electric Steam Boiler
The process of steam generation starts when the feed water enters the steam drum through both internal tubes and the tubes that surround the furnace. The system of tubes that surrounds the furnace is known as waterwall or floor tubes. The feed water gets heated when passed through these tubes. Addition to this, there are Large-bore downcomer tubes that passes outside of the furnace and are used to circulate water between the drums, to which the tubes are attached from outside of the furnace.
The steam produced in the steam drum is known as wet or saturated steam. This steam cannot be used directly as it contains high amounts of moisture. To make this steam usable, it is first dried and heated with the help of a superheater located within the boiler. Once all the moisture content is removed from the steam, the superheated steam can be supplied to other systems. It is utmostly important to monitor and control the temperature of the superheated steam, or else it can cause damage to the systems to which it is supplied. For this reason, an implement known as an attemperator is used. The attemperator is a kind of cooler which is used to cool down the superheated steam to the right temperature. Thus, all the steam used in various system is taken out from the main steam drum of the boiler.
The energy from the fuel burning are used for various other purposes, the main two are as follows:
For heating feed water to produce steam
For superheating the steam from the boiler drum
To increase the efficiency of the boiler, the feed water that enters the boiler is pre-heated with the help of an economizer through which the feed water passes before entering the boiler. The exhaust gas of the boiler is also put to use by making it pass over an air heater, which heats up the combustion air entering the furnace. Thus, even the energy exhausted from the boiler is not allowed to go waste, which increases the overall efficiency of the system.
All these boilers are fitted with various safety fittings and control systems to monitor and control various aspects such as fuel oil flow rate, flow of combustion air, and feed water supply. All these systems should work in co-ordination to supply the amount of steam required by various system. The boiler is also provided with various mountings to ensure safe operation of the boiler.